What is Porosity in Welding: Essential Tips for Getting Flawless Welds
What is Porosity in Welding: Essential Tips for Getting Flawless Welds
Blog Article
The Scientific Research Behind Porosity: A Comprehensive Guide for Welders and Fabricators
Recognizing the intricate systems behind porosity in welding is critical for welders and fabricators aiming for flawless workmanship. From the make-up of the base products to the intricacies of the welding process itself, a plethora of variables conspire to either intensify or reduce the existence of porosity.
Comprehending Porosity in Welding
FIRST SENTENCE:
Exam of porosity in welding discloses critical understandings right into the integrity and quality of the weld joint. Porosity, characterized by the visibility of dental caries or gaps within the weld metal, is an usual problem in welding procedures. These spaces, if not correctly addressed, can jeopardize the architectural integrity and mechanical homes of the weld, resulting in prospective failures in the ended up item.
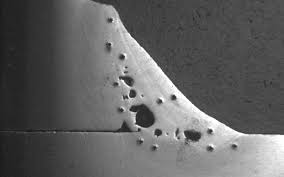
To discover and measure porosity, non-destructive testing approaches such as ultrasonic screening or X-ray evaluation are commonly utilized. These techniques permit the recognition of inner issues without endangering the stability of the weld. By analyzing the dimension, shape, and circulation of porosity within a weld, welders can make educated choices to improve their welding processes and achieve sounder weld joints.

Factors Affecting Porosity Development
The incident of porosity in welding is affected by a myriad of aspects, varying from gas protecting efficiency to the intricacies of welding criterion setups. One vital element adding to porosity development is insufficient gas shielding. When the shielding gas, usually argon or carbon dioxide, is not properly covering the weld swimming pool, climatic gases like oxygen and nitrogen can contaminate the liquified steel, leading to porosity. Furthermore, the cleanliness of the base products plays a considerable role. Pollutants such as rust, oil, or dampness can vaporize during welding, producing gas pockets within the weld. Welding criteria, consisting of voltage, current, take a trip speed, and electrode type, additionally effect porosity development. Utilizing inappropriate settings can create too much spatter or heat input, which consequently can cause porosity. Additionally, the welding method employed, such as gas steel arc welding (GMAW) or protected steel arc welding (SMAW), can affect porosity formation as a result of variants in heat circulation and gas protection. Recognizing and regulating these elements are necessary for minimizing porosity in welding procedures.
Effects of Porosity on Weld Quality
The existence of porosity likewise damages the weld's resistance go to this website to corrosion, as the trapped air or gases within the voids can respond with the surrounding setting, leading to destruction over time. Additionally, porosity can impede the weld's capacity to endure stress or impact, more endangering the general quality and reliability of the bonded structure. In crucial applications such as aerospace, vehicle, or structural buildings, where safety and durability are critical, the destructive impacts of porosity on weld top quality can have serious consequences, stressing the relevance of Web Site lessening porosity with proper welding methods and procedures.
Strategies to Minimize Porosity
To boost the quality of bonded joints and ensure architectural integrity, welders and producers use specific methods focused on lowering the formation of spaces and dental caries within the material during the welding procedure. One reliable method to minimize porosity is to make sure correct product prep work. This includes extensive cleansing of the base steel to remove any type of pollutants such as oil, oil, or wetness that might add to porosity development. In addition, utilizing the ideal welding criteria, such as the proper voltage, existing, and take a trip rate, is crucial in preventing porosity. Maintaining a regular arc size and angle throughout welding additionally aids lower the likelihood of porosity.

Making use of the suitable welding technique, such as back-stepping or using a weaving movement, can likewise aid disperse heat equally and decrease the opportunities of porosity development. By carrying out these techniques, welders can properly lessen porosity and create top quality bonded joints.
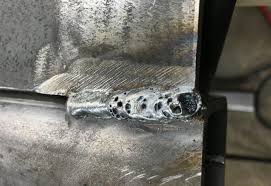
Advanced Solutions for Porosity Control
Executing sophisticated modern technologies and innovative go to these guys approaches plays a critical duty in achieving exceptional control over porosity in welding procedures. In addition, utilizing advanced welding techniques such as pulsed MIG welding or customized atmosphere welding can likewise assist minimize porosity problems.
An additional sophisticated remedy involves the use of sophisticated welding devices. Utilizing devices with integrated attributes like waveform control and advanced power sources can boost weld quality and reduce porosity risks. The application of automated welding systems with exact control over specifications can substantially decrease porosity defects.
Additionally, integrating sophisticated tracking and examination technologies such as real-time X-ray imaging or automated ultrasonic testing can help in finding porosity early in the welding procedure, enabling immediate restorative actions. In general, integrating these sophisticated remedies can substantially improve porosity control and enhance the overall quality of welded components.
Conclusion
In final thought, comprehending the science behind porosity in welding is essential for welders and makers to generate top notch welds - What is Porosity. Advanced options for porosity control can even more enhance the welding procedure and make sure a strong and dependable weld.
Report this page